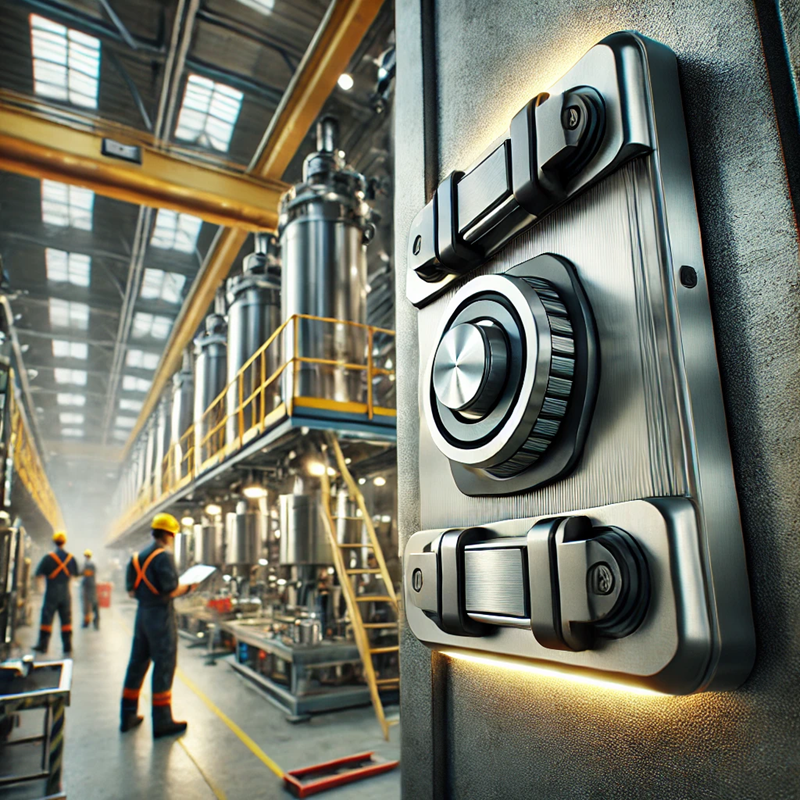
In industrial operations, every minute of downtime translates into lost productivity, higher labor costs, and missed deadlines. Traditional mechanical fastening systems—relying on hinges, screws, and latches—often contribute to increased maintenance expenses due to wear, misalignment, corrosion, and mechanical failure over time.
Magnetic latches offer a smart, efficient alternative that not only improves operational efficiency but also significantly reduces long-term maintenance costs. Their simplicity, durability, and reliability make them an attractive solution for a wide range of industries, from manufacturing and logistics to food processing and medical equipment production.
1. Eliminating Mechanical Wear and Tear
Traditional latches and fasteners involve multiple moving parts that are prone to mechanical wear due to continuous use, friction, and environmental exposure. Over time, springs weaken, hinges corrode, and parts misalign, requiring regular repairs or replacements.
Magnetic latches, on the other hand, have no mechanical friction points. Their non-contact operation reduces the risk of:
- Component fatigue
- Misalignment issues
- Part failure due to repetitive use
This drastically lowers the need for preventive maintenance and extends the service life of doors, panels, and access points across industrial facilities.
2. Speeding Up Inspection and Servicing
In many industrial settings, machinery panels, electrical enclosures, and inspection ports require frequent access for maintenance. Traditional mechanical latches often slow down this process because they:
- Require tools for opening and closing
- Can corrode or jam over time
- Need alignment or adjustment after repeated use
Magnetic latches enable tool-free, instant access to critical areas. Maintenance crews can quickly open panels without searching for the right tools, minimizing downtime during inspections, troubleshooting, and repairs. Faster access not only reduces labor hours but also enables quicker response to operational issues, keeping equipment running smoothly.
3. Superior Resistance to Environmental Factors
Industrial environments often expose components to dust, moisture, chemicals, and temperature fluctuations—all of which can degrade traditional mechanical fasteners.
Magnetic latches are:
- Naturally resistant to corrosion (especially when made with stainless steel or coated magnets)
- Unaffected by dust and debris buildup
- Reliable across a wide temperature range
Their resistance to environmental wear reduces the frequency of replacements and ensures longer intervals between maintenance cycles, leading to lower operational costs.
4. Reducing Inventory and Replacement Costs
Traditional latches require warehouses to stock various spare parts (springs, hinges, locks) for regular replacements. Magnetic latches, due to their longer lifespan and minimal maintenance requirements, allow facilities to simplify their inventory and lower procurement costs.
Fewer replacement parts mean less capital tied up in spare components, freeing up budget for other operational needs.
Conclusion
Magnetic latches offer more than just ease of use—they deliver real, measurable cost savings by eliminating mechanical failures, speeding up servicing, improving environmental resilience, and reducing inventory demands.
For industries striving to minimize downtime, extend equipment lifespan, and lower maintenance costs, magnetic latching systems are a smart investment that pays off in both the short and long term. As industrial operations continue to push for higher efficiency, magnetic latches will play an increasingly important role in maintenance strategies worldwide.